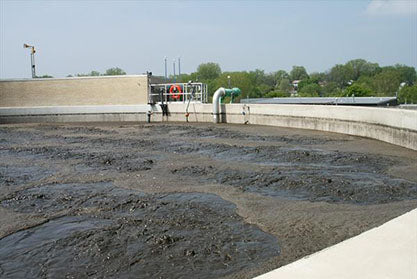
Case Study: Sewer Utility
Problem
The operator of a Sewer Utility faced a growing problem on how to improve efficiency in his plant while dealing with a tightening budget. While hauling costs were a simple fact of life for this small municipal plant, polymer costs seemed quite expensive for the benefit achieved.
Using polymers, a municipal plant operator had to wait 6-7 hours to decant and was pumping once every other month.
Treatment Objectives
- Eliminate polymer usage
- Reduce sludge and the corresponding hauling costs
- Implement a complete natural treatment program to enhance digester efficiency
- Improve overall settling
- Reduce labor costs
The utility decided on an approach utilizing enzymes,bacteria and micro-nutrients.
Chemistry Used
A program was designed implementing three all natural technologies from Great Lakes Bio Systems:
Enzymes: A broad spectrum blend of purified enzymes designed to rapidly speed up the natural bio-degradation process. Enzymes enhance bio-activity by attacking and breaking down organic contaminants found in a municipal waste stream.
Bacteria: A proprietary blend of non-pathogenic naturally occurring microorganisms specifically selected for their advanced sludge digestion capabilities.
Trace Minerals: A complete blend of beneficial micro-nutrients designed to provide both the naturally occurring and augmented bacteria the necessary vitamin supplement to enhance bio-activity, stabilize pH, reduce ammonia and phosphorous which optimizes the system.
Results
With polymer usage, sludge had to be hauled away every two months. A typical decant took six to seven hours. With the implementation of the complete program from Great Lakes Bio Systems, hauling frequency was reduced to every 3 months.
During the summer of 2006, the operator was able to extend this to four months. The decant became much less labor intensive and with the improved settling, this process took less than two hours.
With a hauling frequency of four times annually and with the elimination of the polymer, the utility saved an estimated 35%. This percentage does not include the additional savings achieved by improved labor efficiencies.